Originally posted on 6/2/2018 – Updated on 4/11/2019
It may seem like bundling is something simple, as it consists of placing the fabric in layers to make the cut. However, this stage of preparation for wrapping is very important so that cutting and sewing are done properly.
In this article we will talk about preparing for molding in the fashion industry and how you can optimize this process in your clothing industry. Check it out!
How important is a good dressing?
Before we talk about how you can improve preparation for baking, you need to understand why this process requires care. To begin with, the technique needs to be done correctly, according to the guidelines and needs of each fabric.
That’s because it’s during this stage that proper thread guidance and edge alignment can occur. Thus, it’s possible to prevent defects from reaching the cutting and sewing stages.
What are the best types of dressing?
There are different types of spreading, and they need to be chosen according to characteristics such as available equipment, production needs, textile material used, thread guidance, edge alignment, among others. Now, let’s explore the main types of spreading used in clothing manufacturing:
Pair Spreading
Also known as accordion or zigzag spreading, in pair spreading, the sheets are placed as follows: right side to right side and wrong side to wrong side. The advantage is speed, as this spreading results in two parts of the garment, left and right.
Odd Spreading
When using this spreading, it’s necessary to return to the beginning of the spreading table to start laying out the next sheet, resulting in only one part of each garment. It’s usually used for asymmetrical cuts.
Right side to right side in opposite directions
Fabrics that slide easily, such as velvet and chenille, need to be arranged with the directions in opposite directions, starting from the same end of the table.
This prevents slipping between layers and, consequently, faults in the cutting process.
In addition to knowing which type of spreading to use, according to the Sewability, Use, and Conservation Guide for Fabrics by the Texbrasil Decor Committee, some precautions need to be taken during this stage.
Here are some of them:
- Do not mix batches and shades of fabrics, as this can result in different shades of spread fabrics. If mixing is necessary, ensure that the colors are very distinct so they do not blend during sewing.
- Edge alignment must be done carefully so that the fabric can be well utilized. If folds or wrinkles form, there is a high chance of deformations that cannot be corrected during the sewing stage.
- It’s essential to understand that the number of sheets or layers of fabric is not only related to the quantity of pieces to be produced. They must consider the height of the cutting knife, the thickness of the fabric, and the skill of the cutter.
- It’s important to note that each fabric is analyzed separately because some of them do not have defined positions due to the direction of the pile, shine, or prints.
How to optimize preparation for spreading?
Taking all necessary precautions for a good spreading is not enough if the preparation is not properly carried out. Without proper preparation, fabrics with defects and flaws that affect the quality of the pieces and cause waste can pass through.
With the resurgence of high production, clothing manufacturing companies often confuse process losses with process errors.
As a result, a large volume of raw materials is lost due to lack of information.
In general, companies focus on the measurements of the finished/sewn pieces, but they do not analyze the cause of the problems, which often include variables in their raw materials.
Basic information about raw materials is indispensable for planning/spreading and cutting in a clothing manufacturing process.
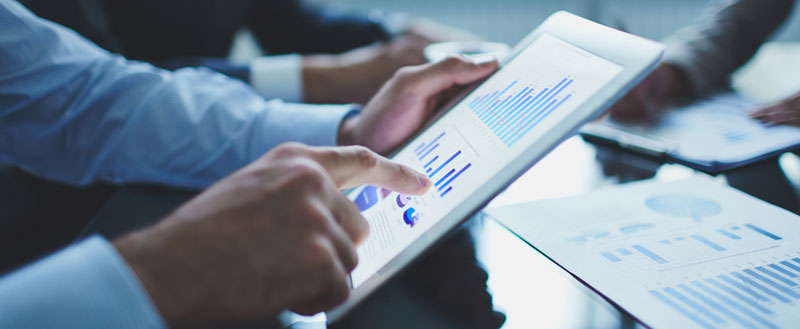
Imagine how clothing manufacturers would benefit if they had real and stable information (width, meters, usable area, weight, yield) for each roll of knit/fabric in their inventory online?
And what if there was the possibility to check inventory information and select the best roll, with the best utilization for each cutting order? What would the gains be if it were no longer necessary to remove a roll from spreading due to manufacturing defects and size variations? All these possibilities are already feasible.
How does spreading preparation work in Industry 4.0?
Although the current process of many clothing manufacturers still consists of purchasing the roll of knit/fabric and then relying on the information on the label generated by the manufacturer, there are already solutions that improve this procedure.
However, the manufacturer itself advises relaxing/resting these articles so that they return to their normal states (without stretching), due to the alteration in the measurements of the roll’s knit/fabric. This means that such measurements are not exact and need to be checked more accurately to avoid process failures.
With the automation of spreading preparation, as soon as the fabrics arrive at the clothing manufacturer, they can go through a Revisor machine that aligns the roll’s edge, analyzes the fabric for defects, and generates a report containing information such as roll classification and defect identification.
https://youtube.com/watch?v=vBOc3HEXJiw
A Sample Washer can also be used to determine the percentage of mesh shrinkage in a much faster and more efficient way. Through it, tests that used to take 3 hours can now be done in just 20 minutes, and only a small amount of fabric is needed to obtain the results.
Then, the fabric can go through a Relaxing machine, which reduces the rest time of the fabric from 24/48 hours to just a few minutes. It also eliminates the process of spreading and rolling up the fabric, in addition to providing the real length and width of the entire roll.
As a result, cutting can be programmed according to the obtained information, including length and width. In other words, no waste, no second-quality pieces, and no losses.
Understanding this compensation is the first step to adapting to the concept of Industry 4.0 because, without the appropriate technology and a personalized plan to automate the entire quality control, relaxation, and data collection process, it becomes difficult to have real information for proper planning.
It’s important to emphasize that high technology in machines and industrial automation optimize variables and allow for the creation of a database of extreme importance for the traceability of raw materials in clothing manufacturing, making the process safer.
Many companies overseas are already completely transforming their production lines and adapting to Industry 4.0. Here in Brazil, some clothing manufacturers have already begun to automate their processes, and due to the benefits it brings, they have already started to see returns. Therefore, it’s important to be aware of market transformations and not fall behind.
If you’re looking for personalized corporate solutions, Delta Equipamentos offers the most efficient ones in the segment. Get in touch with our consultants and clarify your doubts!