Updated on: 04/04/2019
Fabric preparation is a crucial step in textile quality control. Contrary to some beliefs, it starts much earlier than the final product manufacturing process. In fact, it’s essential right at the beginning of production, during the raw material selection phase.
Before using a fabric roll, it’s important to identify potential defects such as holes and flaws. Control allows you to eliminate waste, reduce costs, guarantee the desired quality of parts and map the best suppliers for your textile industry.
In essence, the quality of a fabric roll will influence all the outcomes throughout the production chain and subsequently, the sales of the products.
Hence, it’s essential to maintain textile quality control from the moment a fabric roll is received in your company. Discover now how this process is carried out in the 4.0 manufacturing and what changes and impacts it brings!
What to consider during the quality control of a fabric roll?
Upon receiving the fabric roll, it’s necessary to observe any manufacturing defects and assess its quality. Some standards from the Brazilian Association of Technical Standards (ABNT), such as NBR 13378 and NBR 13175, help identify problems according to the fabric type.
Among the aspects to consider when receiving a fabric roll in your company for textile quality control purposes are:
-
Width and length
To program the fitting of the molds and be able to understand the mesh losses that will occur during cutting, it is essential that the roll mesh has the appropriate width. This criterion will directly affect the production cost of your industry.
-
Imperfections
Lack of thread, frayed weft, stains, frayed mesh and torn selvedge are just some of the factory defects that can be observed in a roll of mesh. These imperfections may cause problems in the parts produced.
-
Grammage
It is through the fabric weight – measured in grams per square meter (g/m²) – that a fabric can be identified as lightweight, medium-weight, or heavyweight.
This criterion may seem trivial, but it makes it easier to choose the needle and sewing thread to be used in garment manufacturing.
How to conduct textile quality control based on data?
After checking the quantity of rolls in a newly arrived order at your company, it’s ideal to immediately verify the metrological regularity, i.e., the width and length of each fabric roll.
The use of technology provides precision in this task, as you can see in this article on quality control in the Industry 4.0 era. Having access to updated data on everything received, with information such as the number of holes and stains per roll, is a basic step for efficient quality control in fabric preparation.
Through intelligent machines like Delta Equipment’s REV150 iConcept View Knit Inspector, it’s easy to inspect fabric rolls. This is because, whether it’s during raw material reception or any other phase of production requiring textile quality control, the Knit Inspector facilitates defect analysis and classification.
https://youtube.com/watch?v=vBOc3HEXJiw
Through it, the equipment operator observes all the problems of each roll and records them in a defect map. This report is then entered into the textile quality control system.
The sorting enables qualitative selection and directs each fabric roll to the product manufacturing process where it will be best utilized. As a result, the manufacturing gains a significant competitive advantage and begins to execute effective quality control.
How to manage the collected data?
Among the greatest benefits of data-focused management are process control and standardization. However, when data is collected, it also needs to be managed and organized according to its functions. This can be done through the implementation of an enterprise resource planning (ERP) system.
Enterprise Resource Planning (ERP), as the original name suggests, allows for the management of a series of tasks by software or people.
Essentially, ERP facilitates the smooth transmission of information. In addition to allowing more assertive decision-making in a much more agile way. With the use of an ERP system, it’s possible to collect and organize data from various stages of the production chain and different sectors of a company.
This ensures that managers have access to real-time performance indicators and can make interventions at any stage or area of production, at the right time.
Why innovate in fabric preparation processes as soon as possible?
Textile companies urgently need innovation in their production quality control processes, including fabric preparation. There are several reasons why clothing manufacturers should adopt Industry 4.0 innovations as soon as possible; here are some of them:
Information based on data is reliable.
It’s not feasible for processing to assume they delivered a quality fabric roll to manufacturing, while manufacturing assumes they received a quality roll. In the end, nobody is certain, and the chances of there being some issue with the fabrics are significant.
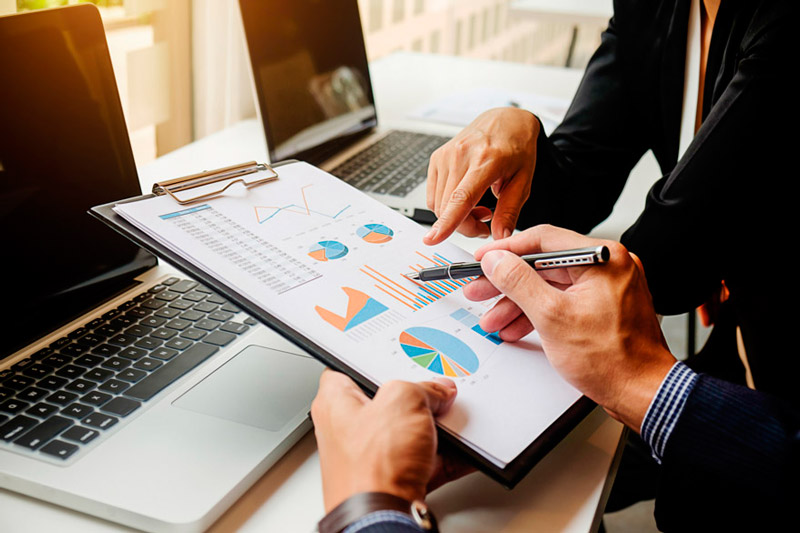
The market has no room for “guesswork”, on the contrary, it demands effective and continuous data control from the entire textile production chain: from processing to manufacturing. Therefore, it’s important to implement modern solutions to produce increasingly efficiently and with higher quality.
Sustainability also needs to be taken into consideration.
Raw material is the gold of manufacturing and cannot be wasted due to lack of quality. Besides reducing costs and “doing more with less” being essential, sustainability is a growing trend, as companies are starting to understand the importance of producing while minimizing environmental impact.
And by sustainability, it’s understood not only creating garment pieces with alternative products but mainly innovating and automating processes to avoid waste and generate fewer residues.
The competition will overrun the industry that doesn’t innovate.
Fabric preparation and the use of automated processes to identify rolls of better quality can increase sales for an industry. Otherwise, the absence of these management mechanisms can make a company lose excellent deals due to the inability to deliver the quality that the customer demands and expects.
A very current example is that of large retailers, which only buy garment pieces that meet their quality standards.
The pursuit of quality improvement has been driven by process automation brought by Industry 4.0 and market demands.
Those who do not adapt tend to become increasingly less competitive or even stagnant.
The result can be very detrimental because, if a manufacturer buys a fabric roll that came full of defects from processing, they will have problems producing the pieces, which will not meet the requirements and will be rejected by large retail chains such as Renner, C&A, Marisa, among others.
Considering that losing contracts with important clients is very detrimental to manufacturing, the textile industry manager needs to be attentive to not end up harming the company.
It’s important to know which raw materials provide more profit.
At first glance, between a fabric roll costing R$ 20.00 per kilogram and one costing R$ 25.00 per kilogram, the one with the lower price seems to cost less to the manufacturer. However, upon closer inspection, it’s possible to realize that it’s not only the price that should be analyzed.
The utilization rate of fabric rolls is also very important, and ignoring it is a major management flaw that causes losses to the textile industry. Unfortunately, this error occurs very frequently because companies tend to analyze the entry price of the raw material when they should be concerned with supervising the cost it represents in their final product.
The problem is that a roll that presents many defects, such as holes and stains, is of poor quality, and its use will have a direct influence on the final result of the manufactured product. Using a raw material with different shades of yellow to make T-shirts, for example, will result in non-uniform pieces.
Having a quality control process at the input of inputs is the basis of any clothing industry that aims to deliver quality as a result of its production process. If the roll does not pass due inspection and its mesh is used, the made t-shirts will have to be sold as second quality products.
+Learn more: What is quality control? How does it work in the textile industry?
However, the value invested in production will remain the same because your industry will use the same structure it would employ to manufacture top-quality shirts, including machinery, employees, working hours, among others.
Therefore, the profit margin of a textile manufacturing starts right here, with fabric preparation. This means that if your company paid R$ 20.00 per kilogram of this fabric, but couldn’t utilize it fully, the ROI of that roll will be much lower than expected at the end of production.
How to calculate the ROI of the fabric supplier?
Return on Investment (ROI) is a metric that can be used to calculate the profit that returned to the company according to the invested value. To calculate the Return on Investment (ROI) of your fabric roll supplier, simply subtract the initially invested value for acquiring the raw material from the profit obtained from selling pieces made with the fabric from the roll. Then, divide the result again by the initial investment value.
The result is the ROI that needs to be constantly monitored so that the company is truly aware of how much it earns with each raw material acquired.
If you work in a textile manufacturing company where managers are still under the illusion that the best mesh roll supplier is the one with the lowest price, it’s time to alert your boss. The company may be accumulating losses. To get you thinking, ask the following questions:
- What is the financial impact of rework?
- Who is your cheapest supplier? Based on what: roll price or quality?
- What is the yield of each kilogram of fabric from your rolls at the end of the production process?
- Does this industry sell all production as first or second quality product?
Remind your company’s manager that it’s possible to return rolls with issues, map out the best suppliers, standardize production, and sell higher quality products. All these measures will have a direct impact on sales, profit, and customer satisfaction.
If they’re still not convinced, present the formula for the cheapest supplier: Cheapest Supplier = Low Price + Yield (Higher Quality Product).
Where can solutions for quality automation in fabric preparation be found?
As you can see, with automation in quality control, decisions in the textile industry become data-driven. This allows for reducing the value gap between standard final pieces and second-quality ones, which are sold well below price (practically just to cover production costs).
Advantages such as a clear view of resources and inputs, full understanding of production, error and fault reduction, and increased productivity are also gained. If you aim to modernize your manufacturing and carry out fabric preparation efficiently, know that this can be achieved through equipment specially designed for the textile sector. Whether in weaving, finishing, or manufacturing.
Delta Equipment offers solutions that cater to the entire production chain. To learn how our equipment can provide the data your industry needs to improve quality, reduce costs, and expand profit margins, reach out to our team.