Providing efficiency in clothing manufacturing is a highly desired goal for production and maintenance supervisors, but often, many believe it requires significant transformations and investments.
In this article, we’ll present a very accessible solution: the reorganization of machine layout. Although it requires planning, it can bring various benefits when done properly. Continue reading to better understand this topic!
What is factory layout?
Factory layout is the physical arrangement used for production flow.
The way it’s planned can result in optimization or delay of the production process. . Therefore, thinking about how the machinery is positioned makes all the difference in the results obtained by clothing manufacturers.
How does it influence efficiency in clothing manufacturing?
When machinery is positioned randomly, there’s a high probability of problems such as transportation bottlenecks, excessive material movement, overwork, and even accidents.
The good layout is one that facilitates movement, always considering the production flow, and the comfort of workers, aiming to minimize material transportation between workstations.
Transportation adds no value to the product; it only moves materials without representing benefits.
There are three main types of layout:
Layout by product/linear
In this type of layout, the machines are fixed, and it’s the product that moves. In some cases, the machine and the operator accompany the product along the line.
It’s a model widely used for mass production of the same product and is advantageous for process automation.
Process/Functional Layout
The process layout is recommended for factories where products have different flows on the same machines.
It’s suitable for industries that have a diversification in the items produced.
Fixed Layout
The product remains stationary while raw materials, machines, equipment, and workers move around it.
It’s commonly used for manufacturing large products such as ships and airplanes.
How to improve the layout in a clothing manufacturing?
To begin with, it’s important to assess the needs of the clothing manufacturer and take care to follow standards, such as the distance between workstations and the crossing of materials and products.
In a textile industry already prepared for advanced manufacturing, the flow typically occurs as follows:
1 – Receipt and qualification of received material
The merchandise is qualified according to the supplier’s technical sheet. A Sample Washer is also used to perform the shrinkage test and dimensional analysis.
When the material fails the test, it’s returned to the supplier due to non-compliance.
+ Find out more: What is quality control? How does it work in the textile industry?
2 – Quality inspection
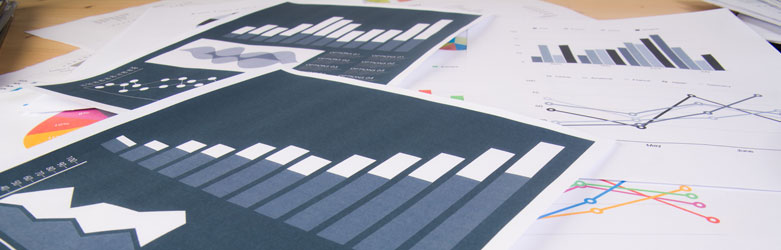
When approved in the previous stage, the fabric undergoes quality inspection at the Reviewer, which generates a defect map and indicates the compromise of the useful area, in addition to analyzing the quality of each roll. When rejected, the raw material returns to the supplier.
+ Find out more: How to modernize quality control in manufacturing?
3 – Mesh rest helps increase manufacturing efficiency
If it passes the quality inspection, the mesh must undergo relaxation. In the traditional method, this step takes up to two days, but with a Mesh Relaxer it only takes a few minutes.
+ Find out more: 6 myths and truths about mesh relaxation
4 – Hive Storage to Achieve Efficiency in Clothing Manufacturing
Although the most common storage methods are done on shelves and racks, with a semi-automatic or automatic Packaging Machine, it’s possible to preserve rolls while optimizing organization and saving space.
5 – Spreading and Cutting
As in the previous stages, where precise measurements and the condition of each roll can be obtained, it’s possible to plan cutting according to the utilization of each roll. Thus, the spreading process is facilitated, and waste is avoided.
While not all clothing manufacturers follow exactly the same pattern, we’ll use the process above as an example.
Regarding the factory layout, imagine how detrimental it would be if the machine responsible for knit relaxation (3rd stage) were located next to the material analysis machine (1st stage) and far from the Revisor machine (2nd stage).
The effort for transporting products from one stage to another would be much greater.
However, if the machine for each stage were positioned correctly, efficiency in clothing manufacturing would increase even more. Less time would be spent on product completion, improving Return on Investment (ROI) results.
Speaking of ROI, calculating this metric is also crucial for maintaining efficiency in clothing manufacturing. To learn more about it, check out this article now and discover how to calculate the ROI of fabric rolls!