Have you heard about the advantages obtained through the entry of garment manufacturing into Industry 4.0? The textile industry has evolved significantly in recent years, and automated processes have already benefited several companies.
With it, it’s possible to optimize processes, increase productivity, and even avoid waste. Want to know how? Continue reading the article and find out!
Mesh preparation and inspection in traditional processes
Traditionally, when purchasing a mesh roll, one must rely solely on the information provided by the manufacturer. However.
There’s no way to qualify and quantify the material or even conduct a physical analysis of the quality standards of each roll manually without losing a significant amount of time in the process.
Usually, inspection is only carried out during spreading.
After that, it’s time to rest/relax the fabric, as it is known that changes in measurements are common and the manufacturer himself indicates that some types of fabric must go through a relaxation process to return to their normal state.
This process takes 24 to 48 hours and requires space on racks or tables so that the fabric can be opened adequately for relaxation.
These are hours when production is not taking place, and human errors can still occur, either by failing to detect any defects in the fabrics and discovering them only after the products are made, or by not properly relaxing the mesh.
The changes brought about by automation
With the automation of the process, all these steps are carried out much more quickly and without errors.
This is because the available equipment offers various solutions to the problems present in the traditional method of preparing and reviewing meshes.
To begin with, when the product arrives at the industry, instead of relying solely on the information provided by the manufacturer, it is now possible to use a Mesh and Fabric Inspector.
https://youtube.com/watch?v=vBOc3HEXJiw
It can monitor characteristics such as width and length, has a synchronization and stretching system, and has a system that ensures the quality of the roll.
It also generates a defect map, indicating the compromise of the fabrics’ useful area.
This data is collected and stored, and inputs that are not approved can be returned to the supplier due to non-conformity.
Then, fabrics that do not need to be relaxed go to storage, and those that need to go through the relaxation process can pass through a Mesh Relaxer.
This equipment completely eliminates the need to have a place to let the mesh rest.
In less than ten minutes, it performs the roll relaxation process and also conditions the climate, generating data on length, width, and side cutting area.
The advantages obtained by manufacturing in the 4.0 industry
In addition to obtaining accurate information about width, useful area, grammage, and yield in an online database, it is possible to avoid retracting the roll from the spread, whether due to measurement variations or manufacturing defects.
Through the control of this data, it is also possible to detect when the raw material is not provided with the necessary quality and, if necessary, replace the supplier.
This avoids the production of items with low-quality meshes and, consequently, the manufacturing of second-quality pieces, which need to be offered at lower prices and generate revenue loss.
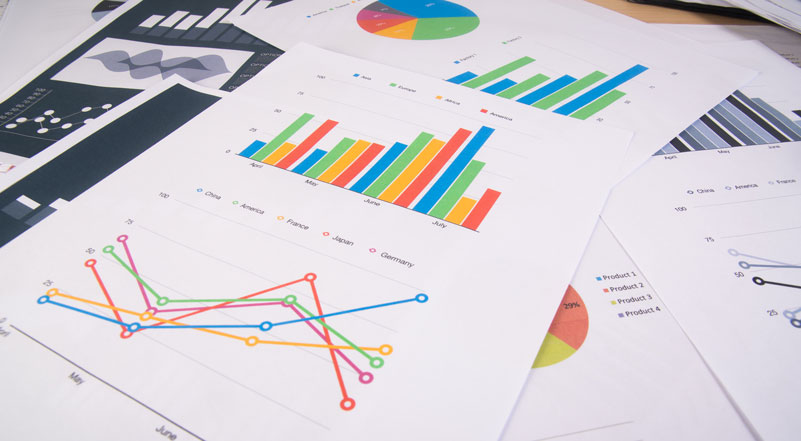
The standardization of products, the quality obtained, the reduction of failures and the increase in productivity are natural consequences of the modernization of manufacturing industry 4.0.
However, for them to function properly, it is not enough to just invest in machinery, it is important to ensure that suppliers provide quality raw materials and train the team so that everyone understands the importance of quality control for the textile industry.
Finally, it’s always necessary to monitor the progress of production in order to provide feedback, both negative and positive, about the items produced so that production becomes increasingly optimized.
Just as it happened in other sectors where technology emerged to enhance processes.
Manufacturers that do not keep up with the evolution of processes will end up losing competitiveness, and their processes will gradually become outdated.
Clothing manufacturers that do not keep up with the evolution of processes will end up losing competitiveness and their processes will gradually become outdated.
Consumers increasingly seek quality and good value for money. With competition increasing every day, there is no longer room for errors in processes, making investment in production and entry into the 4.0 industry a requirement to stay in the market.
If you are interested in the topic and wish to invest in more modern processes, discover right now how to modernize quality control in manufacturing!